catalyst converter- metallic honeycomb substrate
The metallic honeycomb substrate in catalyst converter of vehicle is a newly developed superior substrate to overcome the inherent weakness of ceramic honeycomb substrate. Nowadays people has realized that motorcycle, general-purpose engine must meet National emission standard¢ó&¢ô and the luxury gasoline car and big commercial vehicle must meet National standard ¢ô&¢ơ. Metallic honeycomb substrate is the best technical solution and the metallic honeycomb substrate converter is the best choice for engine emission cleanliness.
RICHLEO develops and produces the metallic honeycomb substrate of catalyst converter on the basis of vacuum brazing technology and environmental protection products production. It use special anti high temperature stainless steel and advanced vacuum welding technology. The products meet the demand to produce emission cleanliness equipments for various types of vehicles and motorcycles. Metallic honeycomb substrate is made of tube body, spacer plate and corrugated plate. The corrugated plate and spacer plate is overlapped and wound up in a core, then places the core in the metal tube and braze the contact area between corrugated plate and spacer plate and the contact area between the outer ring of coil and the inner wall of tube.
The geometric surface area is bigger with higher catalyst efficiency and thus decreases vehicle emission obviously. It will improve the engine output power and reduce the fuel consumption as the exhaust resistance is lower. It can ignite rapidly to reduce the emission pollution of engine ignition as the heat capacity is low. And it has good mechanical endurance, vibration proof and thermal shock resistance.
It is the best substrate for catalyst converter of motorcycle and moped.
Honeycomb has many options from 100PSI to 900PSI and can be customized according to customer¡¯s requirements.
Core advantage: The well experienced senior expert team of RICHLEO developed the serial products of metallic honeycomb substrate and set up the advanced and automatic facilities of inspection and manufacturing with great production capacity and reliable quality. It shows at the below aspects:
1. No quality problems of raw material embrittlerment and even crack.
2. Better performance of anti-pressure and anti-vibration and quicker heat transfer, lower pressure resistance, bigger specific surface area and easy to install etc.
3. The strip foil is cleaned strictly by ultrasonic wave before production to remove oxide film effectively, and pressed into proper corrugation by special hydraulic machine.
4.The extensive bursts of special brazing material enlarge the whole brazing area to its upmost with the specific brazing material and advanced vacumm brazing welding process. It reduces the influence caused by the brazing material covering on the material surface.
5. As it is transversal structure, the channel surface has transversal corrugations to make the gas flow in turbulent status. It increases the effective reaction between exhaust gas and the surface catalyst of channel and improve the cleanliness efficiency of catalyst.
The High-low temperature tests result comparison of RICHLEO to the similar products from abroad have approved that the quality of the RICHLEO brazed metallic substrates reach to the same level with Emitec from Germany.
See below for the comparison details of the tests.
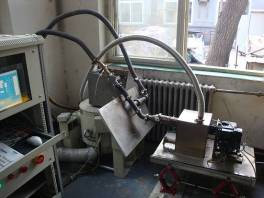
